In the ever-evolving landscape of manufacturing, the efficiency and precision of milling machines play a crucial role. Power feed systems have emerged as a game-changer, allowing for enhanced performance through motor-driven mechanisms. This article delves into the workings of power feed systems, how they boost productivity, and real-world applications demonstrating their advantages.
Know-Why
Power feed systems operate on a straightforward yet effective principle. At the core of this system is an electric motor that drives the feed mechanism, allowing for controlled movement of the workpiece. Unlike manual feeding, which can lead to inconsistencies, power feed provides a consistent feed rate, ensuring uniformity across all machined parts.
The system typically consists of a motor connected to gears that convert rotational motion into linear motion, moving the workpiece along the cutting tool. Advanced control mechanisms, including programmable settings, allow operators to adjust feed rates to suit specific machining tasks. This versatility is particularly beneficial when working with various materials and thicknesses.
Improvement Efficiency
One of the most significant advantages of implementing power feed is the enhancement of production efficiency. By automating the feed process, operators can reduce the physical strain associated with manual handling, resulting in less fatigue and higher output. Moreover, power feed systems contribute to improved machining accuracy, minimizing human error and ensuring that each component meets stringent specifications.
For instance, a study conducted in a manufacturing facility revealed that the introduction of power feed increased production rates by approximately 30%. The ability to maintain a consistent feed rate directly correlated with a reduction in scrap parts and improved overall quality.
Application Case
To illustrate the practical benefits of power feed, consider a company specializing in automotive components. After integrating a power feed system into their milling operations, they reported significant improvements in both efficiency and product quality. The system enabled them to produce parts with tight tolerances consistently, leading to positive feedback from clients and a competitive edge in the market.
Another example can be found in a woodworking shop utilizing a spindle moulder power feed. By automating the feeding process, the shop increased output while ensuring precision in cuts, demonstrating the versatility of power feed systems across different industries.
Power feed systems are revolutionizing the way milling machines operate, offering enhanced efficiency, improved precision, and increased productivity. As technology continues to advance, more manufacturers should consider integrating power feed solutions to stay competitive and meet the evolving demands of the market.
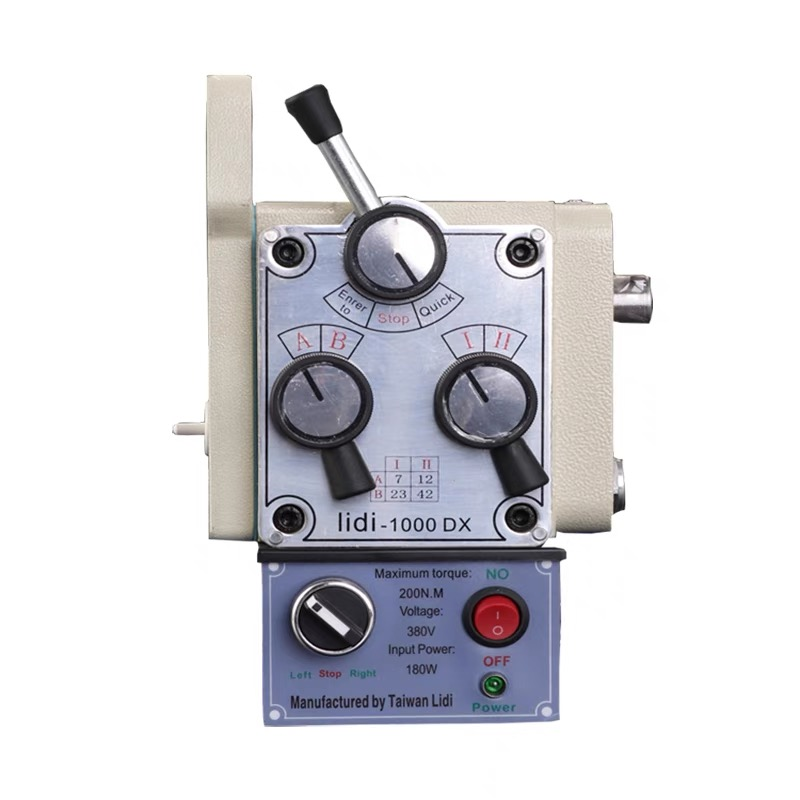
Post time: Oct-12-2024