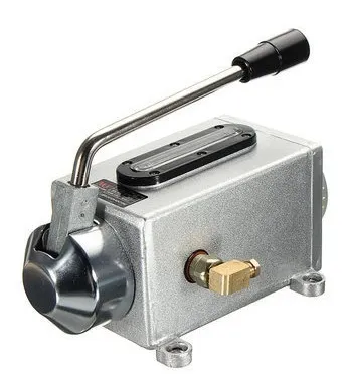
When it comes to selecting an oil pump, several critical factors must be considered to ensure optimal performance and reliability. This guide will delve into the types of media an oil pump can handle, how to determine its flow rate and maximum pressure, the essential material requirements for manufacturing, and key maintenance and care considerations.
**Types of Media an Oil Pump Can Handle**
Oil pumps are designed to handle a variety of fluids based on their construction and intended application. The most common media include:
- **Mineral Oils**: Typically used for general lubrication purposes.
- **Synthetic Oils**: Suitable for high-performance applications where mineral oils may not provide adequate protection.
- **Fuel Oils**: Such as diesel or gasoline, depending on the pump's construction.
- **Coolants**: For machinery requiring temperature regulation.
Each type of fluid has specific characteristics, such as viscosity and corrosiveness, that influence the pump's design and material requirements. It is crucial to match the pump with the type of fluid it will be handling to ensure efficient operation and longevity.
**Determining Flow Rate and Maximum Pressure**
Selecting an oil pump with the correct flow rate and maximum pressure is essential for its performance and reliability:
- **Flow Rate**: This is measured in liters per minute (LPM) or gallons per minute (GPM). It must meet the requirements of the lubrication circuit to ensure that the system receives adequate lubrication. This can be determined based on the operational needs of the machinery or system being serviced.
- **Maximum Pressure**: This indicates the highest pressure the pump can handle without failure. It should be higher than the system's maximum operating pressure to prevent overloading and potential damage.
To determine these specifications, review the machinery or system’s requirements and consult with pump manufacturers to select a pump that matches these criteria.
**Material Requirements for Oil Pumps**
The materials used in manufacturing an oil pump significantly affect its performance and durability. Key material considerations include:
- **Corrosion Resistance**: Pumps handling aggressive or corrosive fluids require materials such as stainless steel or high-grade alloys to resist corrosion and extend service life.
- **Wear Resistance**: For high-wear applications, materials with excellent wear resistance, such as hardened steel or ceramic coatings, are essential.
- **Temperature Tolerance**: Pumps operating in high-temperature environments need materials capable of withstanding elevated temperatures without degrading.
Ensuring that the oil pump is constructed from suitable materials helps to maintain its efficiency and prevent premature failure.
**Maintenance and Care**
Proper maintenance is vital to prolong the lifespan and efficiency of an oil pump:
- **Regular Inspections**: Regularly check for signs of wear, leaks, or unusual noises. Early detection of issues can prevent more severe problems.
- **Filter Maintenance**: Ensure that filters are clean and replaced as needed to avoid contamination of the pump and the lubricated system.
- **Lubrication**: Follow the manufacturer's guidelines for lubricating the pump to prevent friction and wear.
- **Calibration**: Regularly calibrate the pump to ensure it maintains the correct flow rate and pressure.
By adhering to these maintenance practices, you can significantly enhance the pump’s performance and reliability.
In conclusion, selecting the right oil pump involves understanding the types of media it can handle, accurately determining flow rate and pressure requirements, ensuring proper material selection, and implementing a robust maintenance routine.
#oil pump#220V oil pump#lubrication circuit#lubrication piping#www.metalcnctools.com.
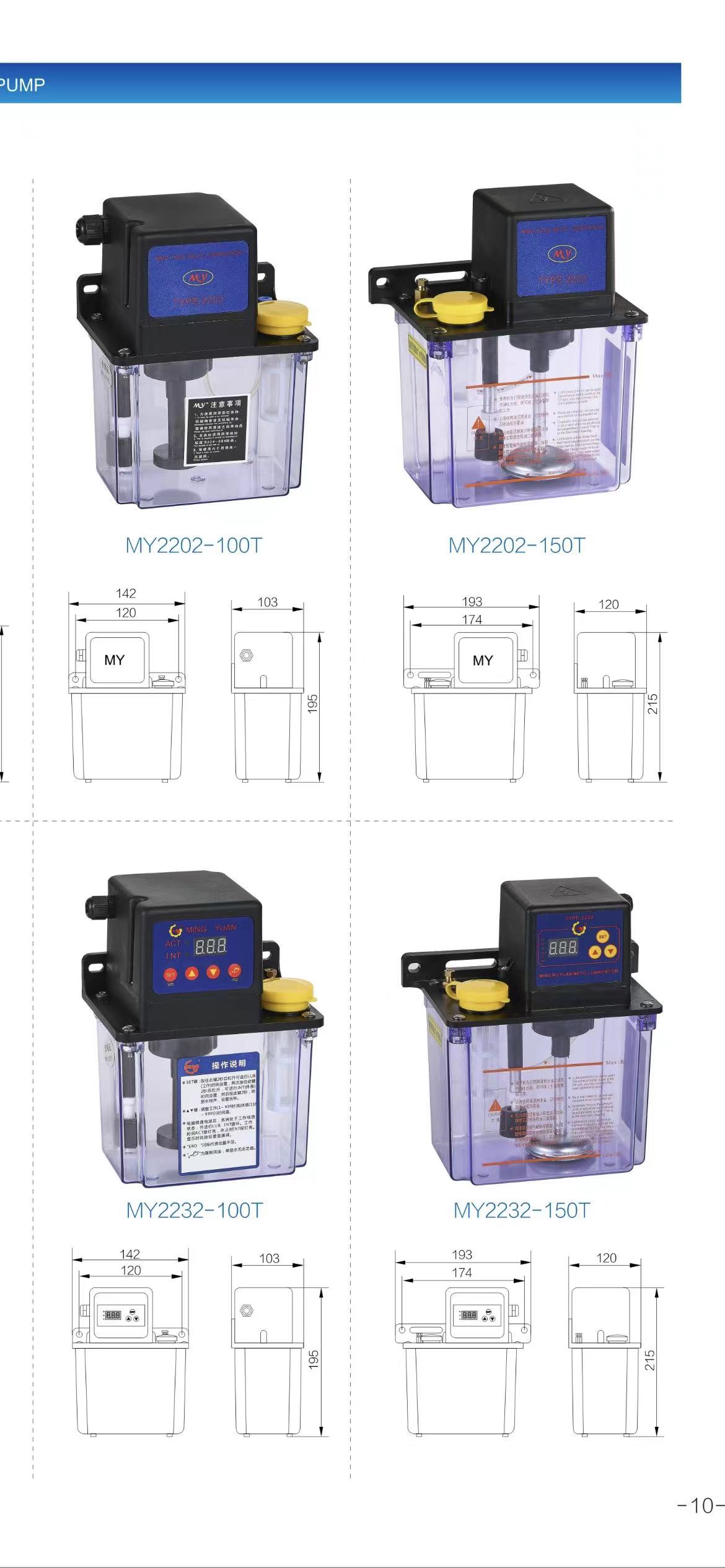
Post time: Aug-12-2024