Clamping tools, particularly clamping kits, are essential components in machining operations, including milling and CNC (Computer Numerical Control) processes. These tools ensure that workpieces remain securely fixed in place during machining, thereby enhancing precision, safety, and efficiency.
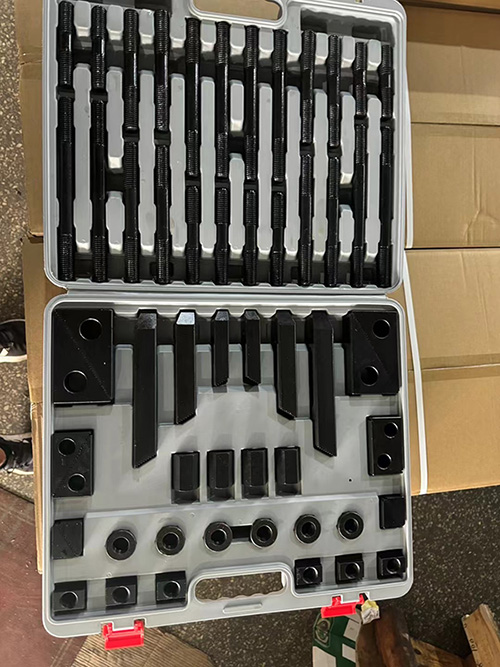
Purpose of Clamping Tools
The primary purpose of clamping tools is to hold workpieces firmly against the machine bed or table. This is crucial for maintaining the accuracy of cuts and preventing any movement that could lead to defects or errors in the final product. Clamping kits, such as 3/8" T-slot clamping kits, 5/8" clamping kits, and 7/16" clamping kits, are specifically designed to accommodate various workpiece sizes and machining requirements.
Basic Principle of Clamping
The basic principle of clamping involves applying a force that secures the workpiece against a stable reference point, usually the machine bed. This is achieved through mechanical means—using bolts, clamps, and T-slot systems—to create a strong grip that prevents movement. The configuration of the clamping system should ensure that the force is evenly distributed across the workpiece, minimizing the risk of deformation during machining.
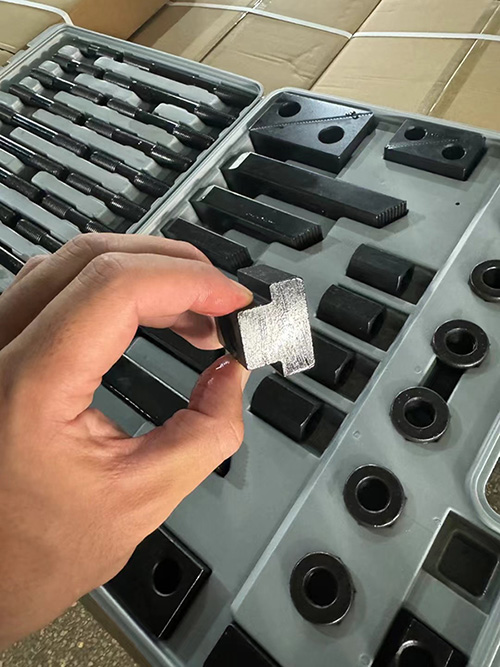

Applications in Milling and CNC Machining
In milling operations, clamping kits are utilized to fix workpieces onto milling machines. For example, the 3/8" T-slot clamping kit is commonly used for standard milling applications, while the 5/8" and 7/16" kits might be favored for larger or more complex workpieces.
In CNC machining, clamping tools are even more critical. The precision required in CNC operations necessitates robust clamping solutions to maintain consistent positioning throughout the automated process. Clamping kits specifically designed for VMC (Vertical Machining Centers) and CNC systems ensure that even during rapid movements, the workpiece remains securely in place.
Considerations for Selecting Clamping Kits
When choosing a clamping kit, engineers should consider several factors:
1. Workpiece Size and Shape: The clamping system must match the dimensions and geometry of the workpiece to provide adequate support.
2. Machining Requirements: Different machining operations may require varying levels of clamping force and configurations.
3. Machine Compatibility: Ensure that the clamping kit is compatible with the specific machine type, whether it’s a standard milling machine or a CNC VMC.

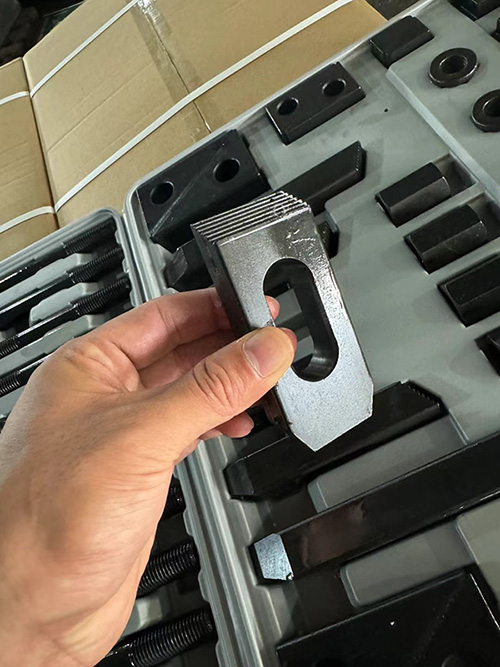
4. Material Considerations:
4.The material of both the workpiece and clamping components can affect the selection. For instance, softer materials may require gentler clamping methods to avoid deformation.
In conclusion, clamping kits are vital for successful machining operations, providing the necessary stability and precision. By understanding the basic principles and applications of these tools, engineers can make informed decisions about selecting the right clamping solutions for their machining needs.
Post time: Sep-21-2024